Aluminum alloys are widely used in various welded structural products due to the characteristics of light weight, high strength, good corrosion resistance, non-magnetic, good formability and good low temperature performance. Reduced by more than 50%. Therefore, in addition to being widely used in aviation, aerospace and electrical engineering, aluminum and aluminum alloys are also increasingly used in the petrochemical industry.
Aluminum and aluminum alloys have the characteristics of strong thermal conductivity, large thermal capacity, large linear expansion coefficient, low melting point and low high-temperature strength. It is difficult to weld. To maintain the quality of welding, not only must we have the correct welding method, but also pay attention to some protective measures .
Aluminum welding methods are roughly divided into three categories according to welding methods:
One type is non-melting electrode argon arc welding, the second type is melting electrode argon arc welding, and the third type is low temperature brazing.
I. Techniques of non-melting electrode argon arc welding skills AC argon arc welding, secondary inverter output, this time you need to master the adjustment of the machine, the choice of materials, and the power for argon arc welding of aluminum alloys Whether the size matches the thickness of the aluminum plate is also crucial.
Second, the method and technique of melting electrode argon arc welding need to select a stable pulse power supply. The wire feeder's wire feed is better. Use graphite tubes and aluminum welding special conductive nozzles and catheters. Try to use coil wire of 1.2 specifications. There are higher hardness aluminum welding wire such as 5356.
Third, Low-temperature brazing methods and application techniques. It is necessary to treat the surface oxide film. The cleanest the better, choose the solder with a lower melting point, such as the lower temperature WEWELDING53 low-temperature aluminum electrode or 303 low-temperature aluminum electrode welding.
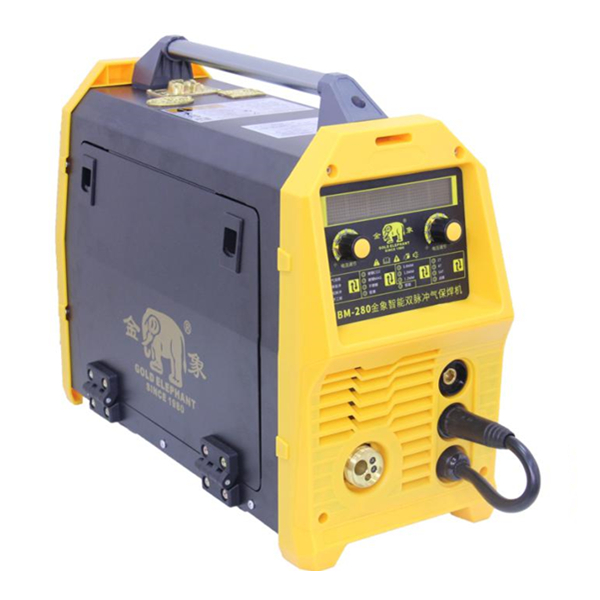